Thiết bị sản xuất nước đá sệt từ nước biển
Công nghệ làm lạnh và làm nước đá sệt trực tiếp từ nước biển là giải pháp bảo quản hải sản sau thu hoạch đem lại hiệu quả cao, chi phí thấp, làm lạnh đều, nhanh chóng. Nước đá sệt được làm trực tiếp từ nước biển có các đặc tính nổi trội như: xốp, mềm, độ lạnh sâu. Khi sử dụng để bảo quản thủy sản, nước đá sệt dễ dàng bao bọc hoàn toàn, không để lại các bọt khí như các phương pháp truyền thống.

Nguyên lý hoạt động:
Nước biển với độ mặn thông thường là 3% được bơm vào khoang (thùng chứa). Bằng phương pháp tuần hoàn, thiết bị sẽ hạ nhiệt lượng nước biển trong khoang (thùng chứa), đưa nhiệt độ xuống thấp nhất là -4oC. Ngoài ra, nước biển còn được dùng để giải nhiệt hệ thống làm lạnh.
Nhiệt độ của đá phù hợp với việc bảo quản hải sản đánh bắt. Đá sệt xốp mịn bao bọc đều bề mặt cá, do vậy giảm được phản ứng thủy phân của tế bào thịt cá. Đặc biệt, đá sệt có thời gian hạ thân nhiệt của cá sau khi đánh bắt nhanh hơn rất nhiều so với phương pháp bảo quản bằng nước đá truyền thống nên chất lượng sản phẩm được nâng lên đáng kể.
Thông số kỹ thuật:
• Công suất máy : 4 tấn nước đá sệt/ngày;
• Máy nén BOCK : HG44E;
• Công suất làm lạnh : 3.100 BTU/giờ;
• Công suất động cơ điện: 16 HP/380V, 3 pha;
• Tốc độ vòng quay : 1.450 vòng/phút;
• Bộ trao đổi nhiệt (SS 316) : 1;
• Nhiệt độ đá sệt : - 40oC;
• Môi chất làm lạnh : R 22;
• Kích thước: 1.219 x 610 x 1.118 mm.
Ưu điểm:
• Nước đá sệt có độ xốp, mềm, không làm kết cứng hải sản, không tạo liên kết giữa vật bảo quản và nước đá nên dễ bốc dỡ; không có cạnh sắc nhọn, không làm hỏng bề mặt hải sản, giảm tỷ lệ hư hỏng.
• Không bị kết băng ngược (kết cứng lại sau khi đã xay hoặc đã cắt thành các cục nhỏ như phương pháp truyền thống).
• Giảm nhẹ tải trọng của tàu, giảm tiêu hao nhiên liệu, giảm chi phí.
• Thiết bị làm lạnh nhanh, sâu và đồng đều; chỉ sản xuất khi cần, giảm tổn thất, chủ động thời gian trên biển.
Dây chuyền sơ chế dược liệu
Dược liệu thô (củ, rễ, quả, cành...) có nguồn gốc từ thực vật, động vật hay khoáng vật chưa qua chế biến theo phương pháp y học cổ truyền. Để sử dụng hiệu quả, phát huy tối đa dược tính và giảm thiểu độc tố, dược liệu cần sơ chế từ dạng thô như: củ, rễ, quả, cành... thành dạng phiến.
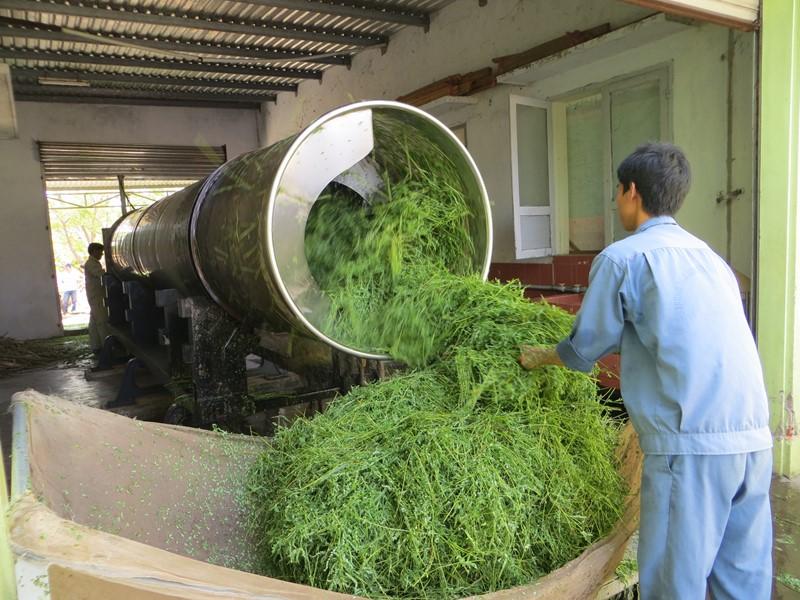
Quy trình sơ chế
• Lựa chọn dược liệu: loại bỏ những bộ phận không dùng, không đủ tiêu chuẩn làm thuốc hay những bộ phận tạo ra những tác dụng không mong muốn; tạo sự đồng đều về kích thước.
• Rửa: làm sạch, làm mềm dược liệu để thuận lợi cho việc bào, thái thành phiến. Giảm tác dụng bất lợi, định hình cho vị thuốc. Rửa bằng nước sạch đến khi hết tạp chất cơ học như: đất, cát, sỏi,… và để ráo nước. Sau khi rửa, không nên chất dược liệu thành đống, dễ bị lên men mốc, phá hủy dược liệu. Với một số dược liệu chứa tinh dầu, có cấu trúc mỏng manh, cần rửa nhanh.
• Ủ mềm: dược liệu rửa sạch, cho vào thùng, chậu nhôm hoặc nhựa hoặc inox. Dùng vải ẩm phủ kín. Trong quá trình ủ nên đảo đều, có thể phun thêm nước đến khi đạt yêu cầu.
• Ngâm: nguyên liệu thô sau khi rửa sạch được ngâm ngập trong nước đến khi đạt yêu cầu. Thường để nước thấm vào dược liệu khoảng 30% (có thể bẻ cong...). Thời gian ngâm tùy thuộc tính chất, mục đích riêng của từng vị thuốc.
• Thái phiến: tùy theo thể chất và tính chất dược liệu, thành phần hóa học của dược liệu, có thể tiến hành ngâm, chưng, đồ hay ủ cho dược liệu mềm. Dùng dao cầu, dao bào, máy thái...để thái thành phiến. Kích thước phiến có độ dài ngắn, dầy mỏng khác nhau, tùy theo loại dược liệu.
• Phơi: làm khô dược liệu, đảm bảo độ thủy phân, giúp cho quá trình bảo quản hoặc giảm tiêu hao năng lượng khi sấy.
• Sấy: nhiệt độ sấy khoảng 70 - 80oC (dược liệu chứa tinh dầu cần khống chế ở nhiệt độ 50 - 60oC). Đối với dược liệu sau khi thái phiến không phơi được nên sấy ở nhiệt độ thấp (khoảng 40oC) sau đó nhiệt độ được tăng dần, để tạo điều kiện cho hơi nước trong dược liệu bốc ra từ từ. Đến khi đạt tới độ ẩm nhất định, nhiệt độ được giảm đi dần dần, kết thúc công đoạn sấy.
Dây chuyền thiết bị
A. Máy rửa dược liệu
Máy dùng để rửa các loại thảo dược trong sản xuất Đông dược và các sản phẩm nông nghiệp. Toàn bộ máy, băng tải bằng inox với độ bền cao. Sục khí khi rửa nên dDược liệu sau khi rửa rất sạch nhờ sục khí trong quá trình rửa. Thiết bị điều khiển bằng PLC và màn hình cảm ứng 5,7 inch. Ngôn ngữ giao tiếp tiếng Việt nên dễ dàng vận hành. Thiết bị dễ dàng vệ sinh, đạt tiêu chuẩn GMP.
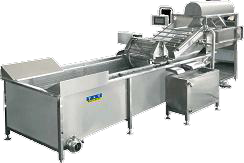
• Năng suất: 700-1.500 kg/giờ;
• Kích thước: 5.370×1.300×1.800 mm;
• Trọng lượng: 950 kg
B. Máy cắt dược liệu
Máy được sử dụùng để cắt tất cả các loại lá, rễ, các loại thảo dược, cành cây và các sản phẩm nông nghiệp. Thiết bị điều khiển bằng PLC và màn hình cảm ứng 5,7 inch. Ngôn ngữ giao tiếp tiếng Việt.
• Năng suất: 20-300 kg/giờ;
• Chiều dài cắt: 0,5-100 mm;
• Kích thước thảo dược sau khi cắt: 0,5 - 30 mm
• Công suất: 2,7 kW;
• Chiều rộng của dao cắt: 264 mm;
• Kích thước: 1.720×810×1.350 mm;
• Trọng lượng: 700 kg
C. Máy phiến lát dược liệu
Máy dùng để thái phiến các loại thảo dược mềm như hành, tỏi, chuối, rễ, củ thành các lát mỏng, kích thước trong khoảng 0,5 – 5 mm.
• Năng suất: 50-200 kg/giờ
• Độ dày của miếng/lát: 0,5 - 5 mm
• Công suất: 1,1 kW
• Kích thước: 1.050×550×1.280 mm
• Trọng lượng: 350kg
D. Tủ sấy băng chuyền
• Dùng để sấy các loại thảo dược và các sản phẩm nông nghiệp. Thiết bị sấy nhanh với băng tải bằng inox, đạt tiêu chuẩn GMP.
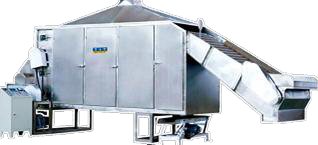
• Năng suất: 100-160 kg/giờ
• Gia nhiệt kiểu dàn hơi nước, tiêu thụ 400 kcal/giờ.
• Diện tích sấy: 16 m2
• Công suất: 5.25 kW
• Kích thước: 8.000×1.900×2.050 mm
• Trọng lượng: 4.000 kg
Công nghệ mạ kẽm nhúng nóng
Mạ kẽm nhúng nóng là công nghệ bảo vệ bề mặt bằng phương pháp phủ lớp kẽm mỏng lên bề mặt kim loại. Lớp kẽm này được tạo thành qua quá trình nhúng kim loại vào bể chứa kẽm nóng chảy. Đây là phương pháp tạo bề mặt chống rỉ phổ biến hiện nay, đã được ứng dụng rộng rãi trong các ngành như: xây dựng, truyền tải điện, giao thông vận tải, nhà máy giấy, nhà máy hóa chất, giàn khoan dầu khí…

Quá trình hình thành lớp mạ kẽm nhúng nóng như sau: sắt hòa tan trong kẽm nóng chảy, kẽm và sắt hình thành hợp chất kim loại, trên bề mặt hợp kim hình thành lớp mạ kẽm tinh khiết.
Ưu điểm
• Tạo lớp bảo vệ các kết cấu kim loại trong các môi trường không khí, biển, khí công nghiệp...
• Phục hồi các chi tiết bị mài mòn: làm mới bề mặt sản phẩm khi bị tác động của các yếu tố môi trường.
• Sản phẩm mạ kẽm có độ bền vượt trội, chống loại các va chạm trong quá trình vận chuyển và sử dụng.
• Bảo vệ ăn mòn điện
• Chi tiết được nhúng hoàn toàn trong bể kẽm nóng chảy, do đó mặt trong và mặt ngoài của sản phẩm có thể được phủ kẽm cùng lúc.
• Mạ kẽm có thể được áp dụng cho rất nhiều mặt hàng khác nhau, từ ốc vít đến những kết cấu to lớn như ống, dầm chữ I…
• Các tính chất cơ học của thép không bị ảnh hưởng bởi mạ kẽm.
Quy trình
• Tẩy nhờn: trong quá trình gia công, các kết cấu thép, ống thép… luôn có một lượng dầu mỡ và các tạp chất bám trên bề mặt chi tiết. Nếu không tẩy rửa lớp kẽm mạ nhúng nóng sẽ không bám hoặc bám không bền, lớp mạ có màu sắc khác thường. Việc tẩy dầu mỡ và các tạp chất được thực hiện trong bể dung dịch kiềm nguội có thêm chất phụ gia.
• Rửa sạch: để rửa sạch kiềm (để không trung hòa khi mang qua bể acid) và váng dầu mỡ khỏi chi tiết.
• Tẩy rỉ lần 1: tẩy phần lớn phần rỉ sét trên bề mặt chi tiết bằng dung dịch acid clohydric (HCl) có nồng độ cao và được cho vào một lượng nhỏ chất phụ gia có tác dụng kìm hãm acid ăn mòn nền thép và hạn chế acid bay hơi.
• Tẩy rỉ lần 2: tẩy triệt để phần rỉ sét còn lại trên bề mặt chi tiết. Nhúng toàn bộ sản phẩm cần tẩy vào dung dịch HCl nồng độ từ 8 - 15%, nhiệt độ 10 - 30oC. Tùy theo mức độ rỉ, thời gian ngâm từ 20 - 60 phút. Rửa sạch acid và các chất còn bám trên bề mặt sản phẩm bằng nước.
• Rửa sạch: rửa sạch acid và clorua sắt hình thành trong quá trình tẩy rỉ khỏi chi tiết.
• Xử lý hóa chất: để bảo vệ bề mặt chi tiết không bị oxy hóa lại trong quá trình sấy và tăng mức độ thấm ướt của kẽm lên bề mặt chi tiết khi mạ nhúng.
• Sấy khô: nhằm làm cho chi tiết bốc phần lớn hơi nước để khi dìm chi tiết vào bể nhúng kẽm không bị phản ứng nổ. Bên cạnh đó, sấy cũng góp phần gia nhiệt sơ bộ cho chi tiết trước khi chuyển sang nhúng kẽm.
• Nhúng kẽm: chi tiết được nhúng trong khoảng 2 - 5 phút, tùy theo trọng lượng, ở nhiệt độ 440 - 450oC. Gạt xỉ ở trên bề mặt kẽm nóng chảy và tiến hành lấy sản phẩm lên trong khoảng từ 1 - 2 phút, kết hợp tạo rung để làm rơi kẽm thừa.
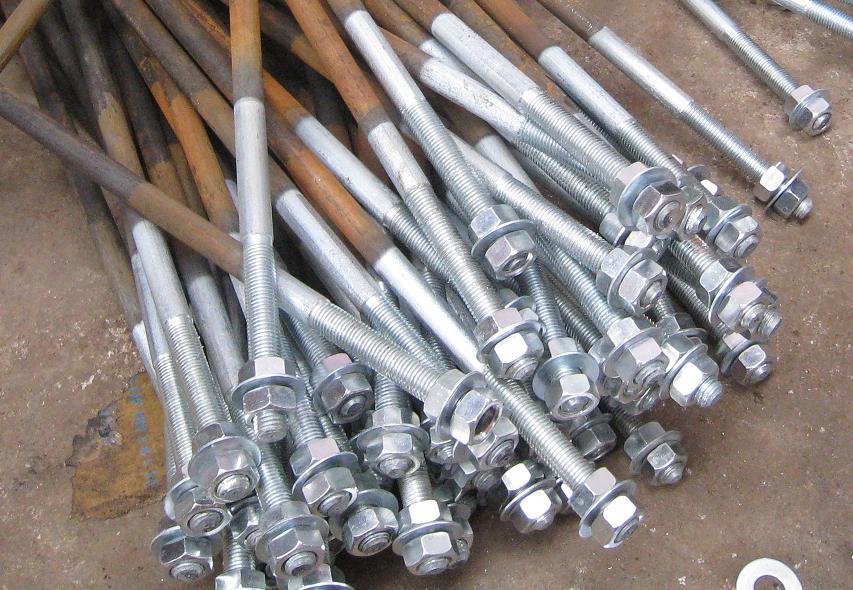
• Làm nguội: để tạo cho lớp kẽm phủ trên bề mặt chi tiết có tổ chức tế vi thích hợp, do đó lớp phủ được bền hơn và bóng sáng hơn.
• Tạo màng thụ động: dùng dung dịch thụ động tạo độ bám chặt cho lớp kẽm phủ trên bề mặt sản phẩm, giúp tăng khả năng chịu lực va đập, bền vững của lớp mạ (nâng cao độ không bong tróc của lớp kẽm phủ trong môi trường tự nhiên).
• Kiểm tra thành phẩm: sản phẩm sau khi nhúng kẽm được tiến hành kiểm tra độ bám dính, chiều dày lớp mạ, màu sắc...
STINFO số 11&12/2016
Tải bài này về tại đây.